P2 decanter centrifuge range High-performance decanter centrifuge for process industries
Applications
The P2 decanter centrifuge is the result of intense focus on per-formance, reliability and sustainability – all at the same time.
It is designed for slurries that are often erosive and aggressive. The P2 range provides the most cost-effective, high-performance solution combined with the lowest power consumption and life cycle costs available within the process industries.
This complete range features a compact, modular design with all critical parts made of wear- and corrosion resistant materials. The result is reliable, continuous operation and easy, trouble-free process control.
Easy to operate, easy to get results
The outstanding features of the P2 design make it easy to accomplish a wide range of performance targets for the applications it operates in.
• Higher separation efficiency, more efficiently
• Greater processing capacity for any given equipment footprint
• Better process control
• Highest level of protection against erosion and corrosion
• Low maintenance costs
• Low energy consumption
• Low life cycle costs
• Capable of the toughest application and safety standards
• Fast and easy mechanical and electrical installation and commissioning.
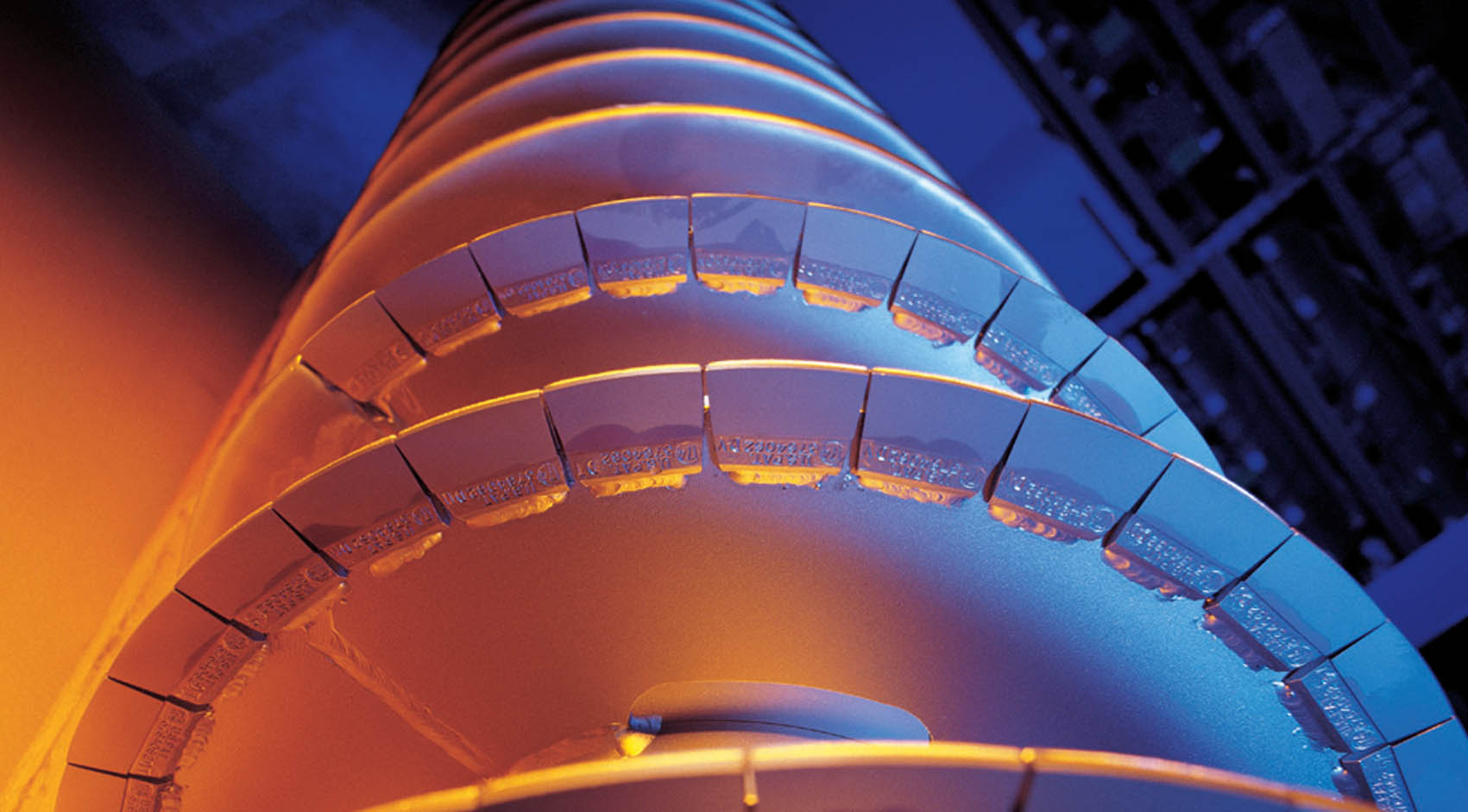
Design
Alfa Laval designed the P2 range of decanter centrifuges with a focus on performance, easy access, reliability and low power consumption as well as noise levels.
The rotating assembly is supported on a compact welded box beam frame with main bearings at both ends. The in-line motor is flanged or foot-mounted on the decanter with brackets for belt tension adjustment. The bowl is driven at the conical end by an electric motor using a V-belt transmission.
The bowl, conveyor, casing, inlet tube, outlets and other parts that come into contact with the process media are made of AISI 316 and Duplex stainless steel.
Working principle
Separation takes place in a horizontal cylindrical bowl equipped with a scroll conveyor. The product is fed into the bowl through a stationary inlet tube and is then smoothly accelerated in a full flow feed zone design. Centrifugal force deposits the solids on the inner surface of the bowl.
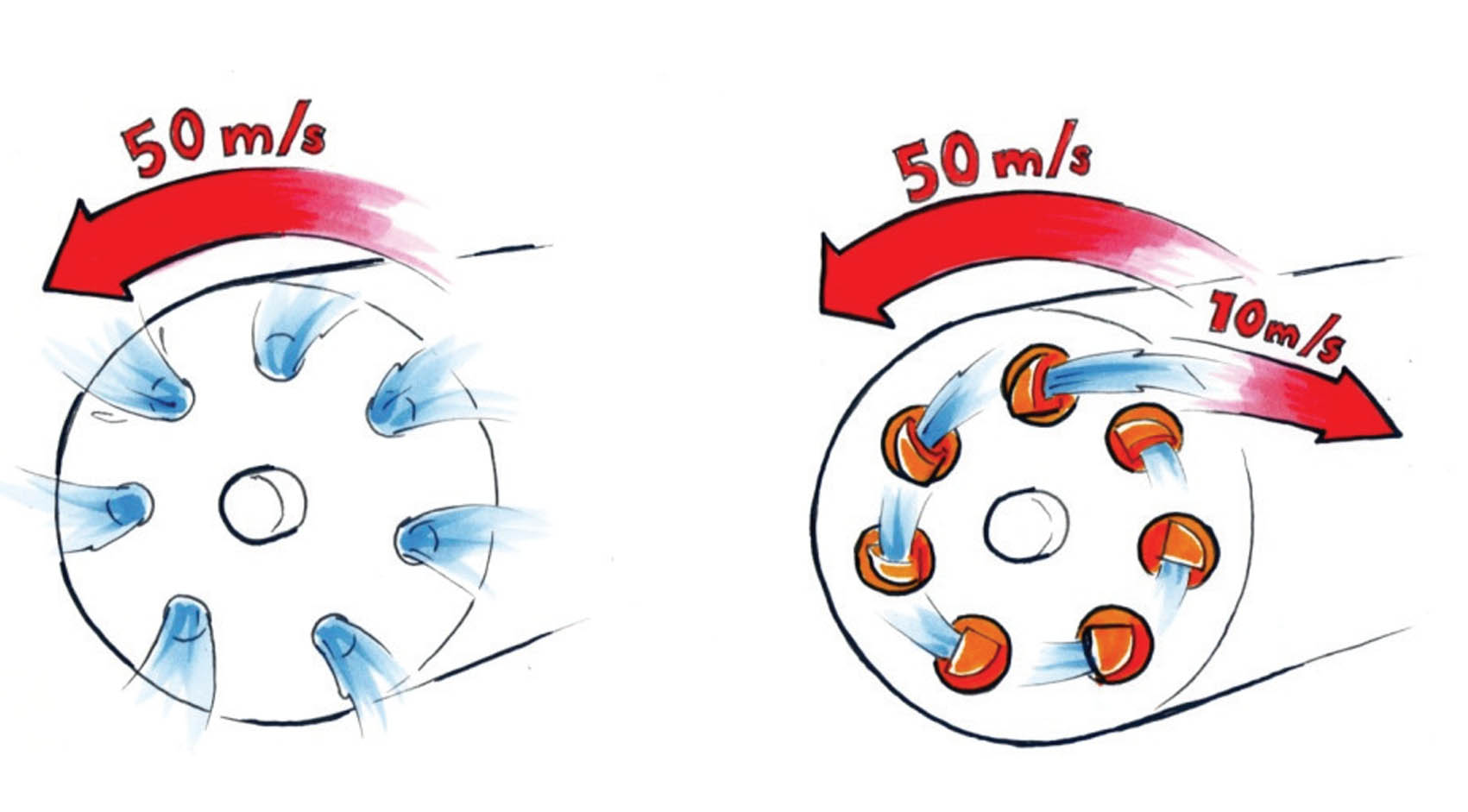
Power consumption becomes power reduction
The bowl can be equipped with specially developed power plates or tubes that harness and exploit hydraulic energy to reduce power consumption still further, while the unique 2Touch control system ensures easy, reliable process optimization.
Some of the discharge velocity from the liquid leaving the unit is captured and re-directed in order to contribute to the bowl rotation. This results in a reduction in the velocity of the dis-charged liquid, which in turn reduces overall power requirements.
Reducing power consumption also means being able to live up to new environmental regulations and helping to support a sustainable environment such as reduction in CO2 emissions.
Direct drive
The drive system that is an integral part of the P2 design was specially developed by Alfa Laval to make it possible to control the conveying speed automatically. This ensures the best possible balance between liquid clarity and solids dryness, irrespective of any variations in the feed flow that may occur.
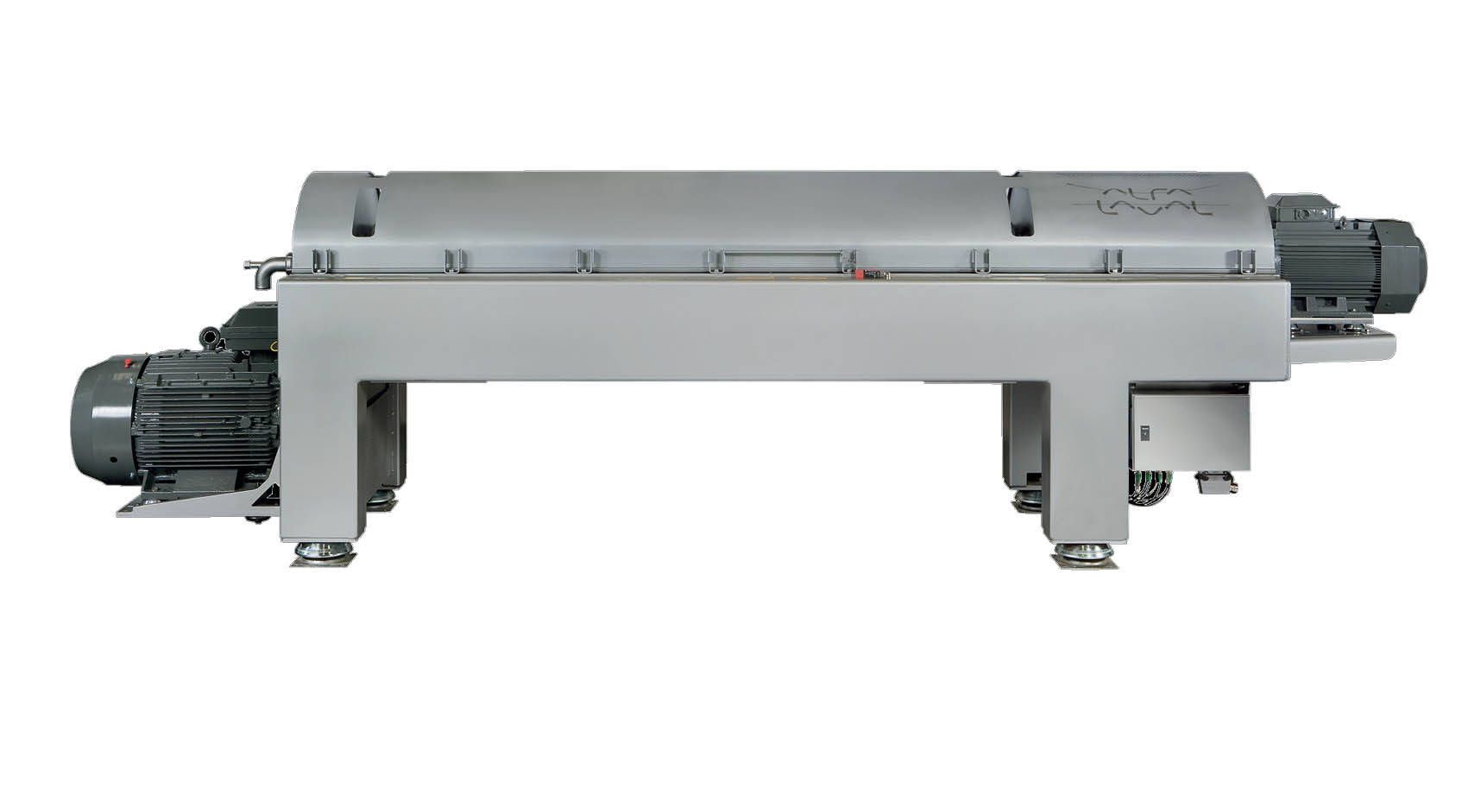
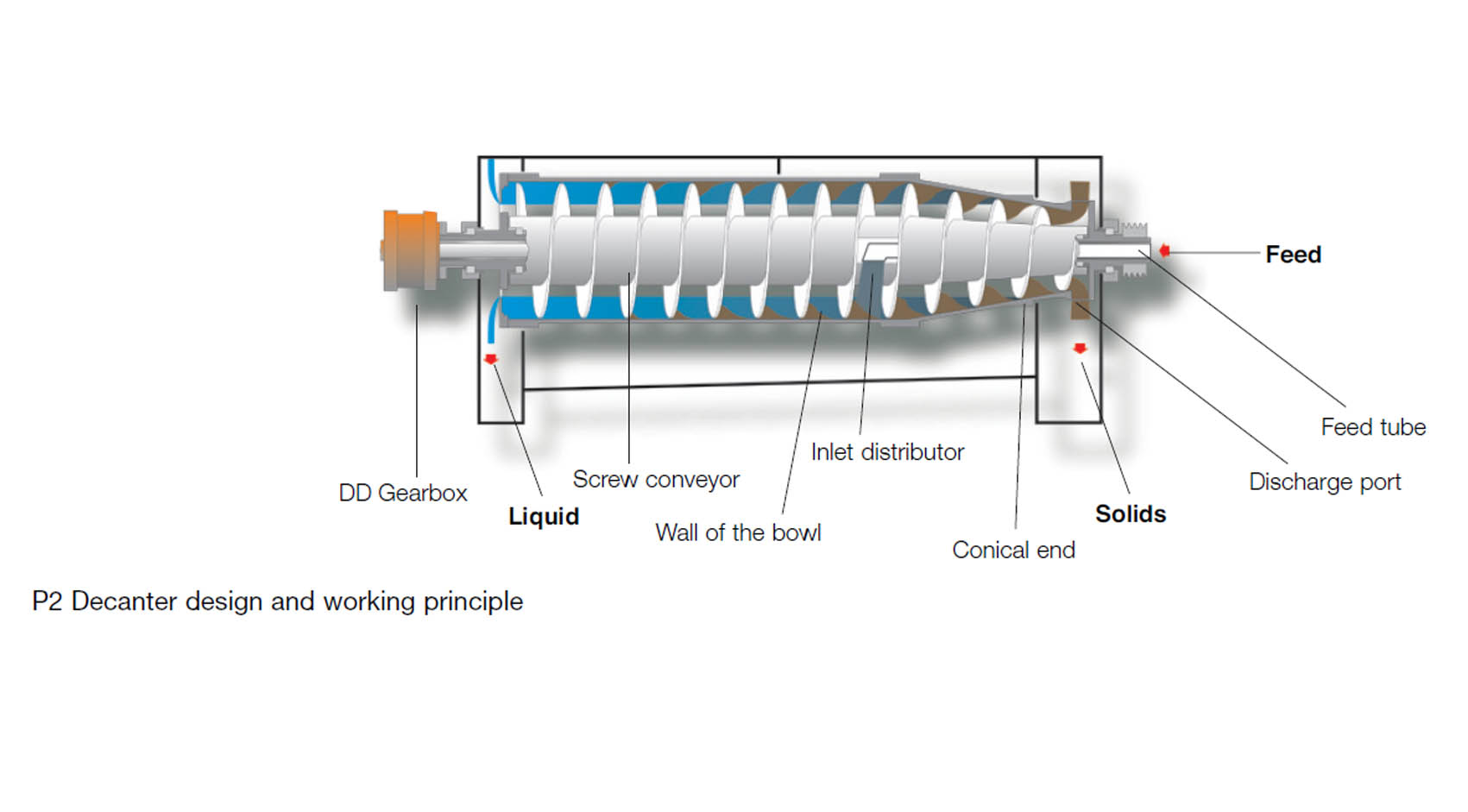
Options
Alfa Laval P2 decanter centrifuges can be tailored to meet specific requirements by varying a range of unique design options pending on the specific application and needs. Among others you can select between:
• Enhanced wear and corrosion protection options – maintenance costs can be reduced still further by selecting even higher degree of wear and corrosion resistant options, for example tungsten carbide tiles.
• Enhanced power saving options – reduce power consumption and minimize impact from power supply interruptions
• Different elastomers and seals to suit resistant to chemical attack and high temperature operation
• Special sealed and purged decanters for processing flammable feed
• 3-phase decanter versions for advanced separation duties
• Control panels with VFD operation of the decanter
• Ex. / ATEX-compliance – available for zones 1, 2 and 22
The conveyor rotates in the same direction as the bowl, but at a different speed, thus moving the solids towards the conical end of the bowl. The solids leave the bowl through the solids discharge openings into the casing.
Separation takes place throughout the entire length of the cylindrical part of the bowl, and the clarified liquid leaves the bowl by flowing over adjustable plate dams into the casing.
Process optimization
The P2 decanter centrifuge can be adjusted to suit specific requirements by varying:
• the bowl speed to ensure the exact G force required for the most efficient separation
• the conveying speed for the best possible balance between liquid clarity and solids dryness
• the pond depth in the bowl for the best possible balance between liquid clarity and solids dryness
• the feed rate – the P2 is designed to handle a wide range of flow rates.
The Direct Drive system comprises an exceptionally efficient gearbox and variable frequency drive, which together avoid exposing the bowl drive to parasitic braking power. It also simplifies the electrical installation and keeps power consumption and CO2 emissions to the absolute minimum. In addition, the Direct Drive is capable of accurate control within the complete range of differentials, with no need for changing belts or pulleys.
2Touch – world-class controls system
Each P2 decanter centrifuge is equipped with a 2Touch control package as standard, pre-installed and factory-tested in conjunction with each particular unit.
The combination of 2Touch control systems and P2 separation technology makes sure you get the most out of any P2 installation, at the same time as keeping costs for installation, commissioning, operation and maintenance to a minimum.
Additional enhancement packages are available for the 2Touch control package. These include:
• Maintenance and training aids, including access to manuals in PDF format and videos about routine maintenance procedures
• Protection against power loss, thus ensuring safe, uninter-
rupted operation, regardless of power dips or outages
• Remote monitoring, response and reporting though external options enabling 2Touch to be integrated into any external system by easy on screen set-up.
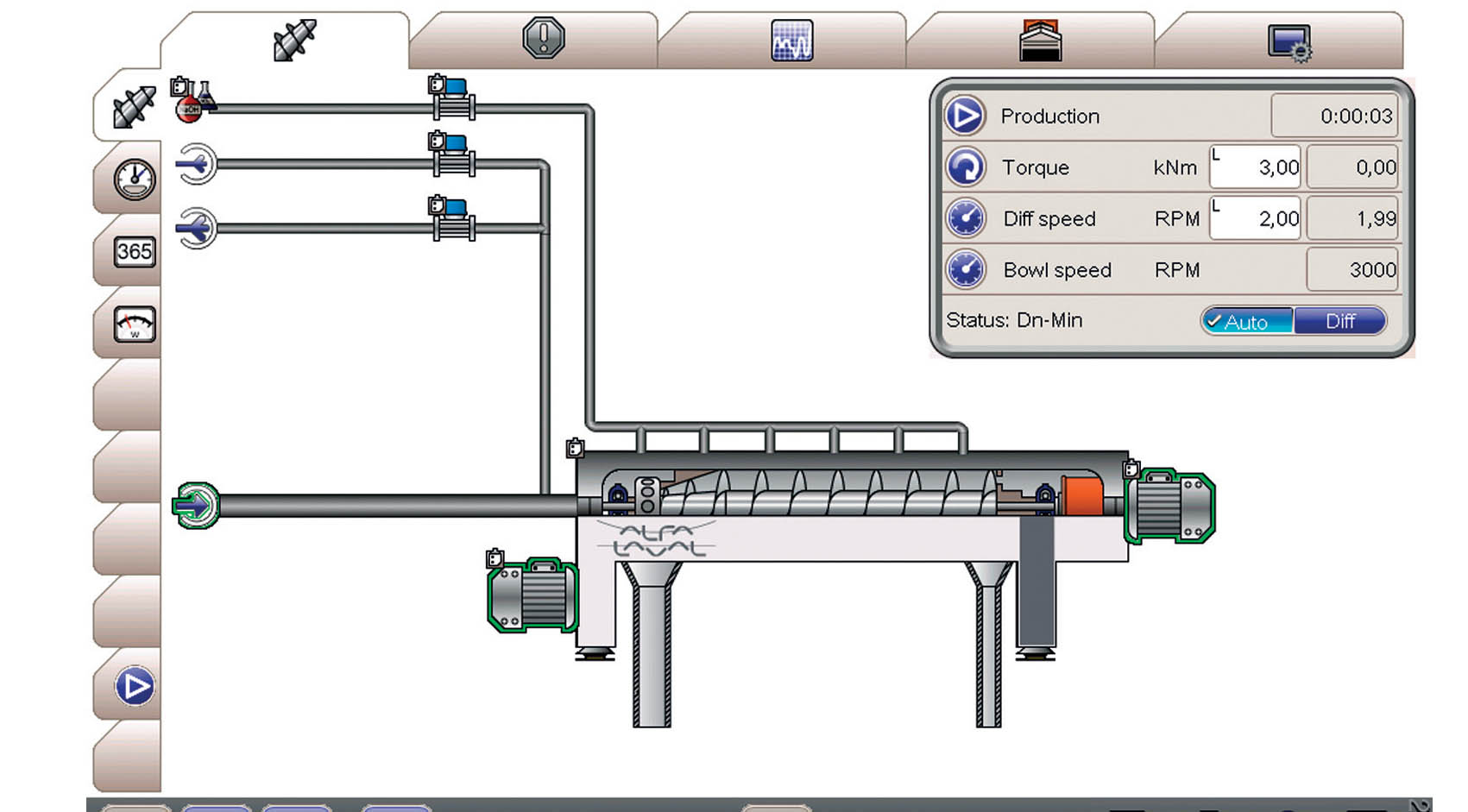
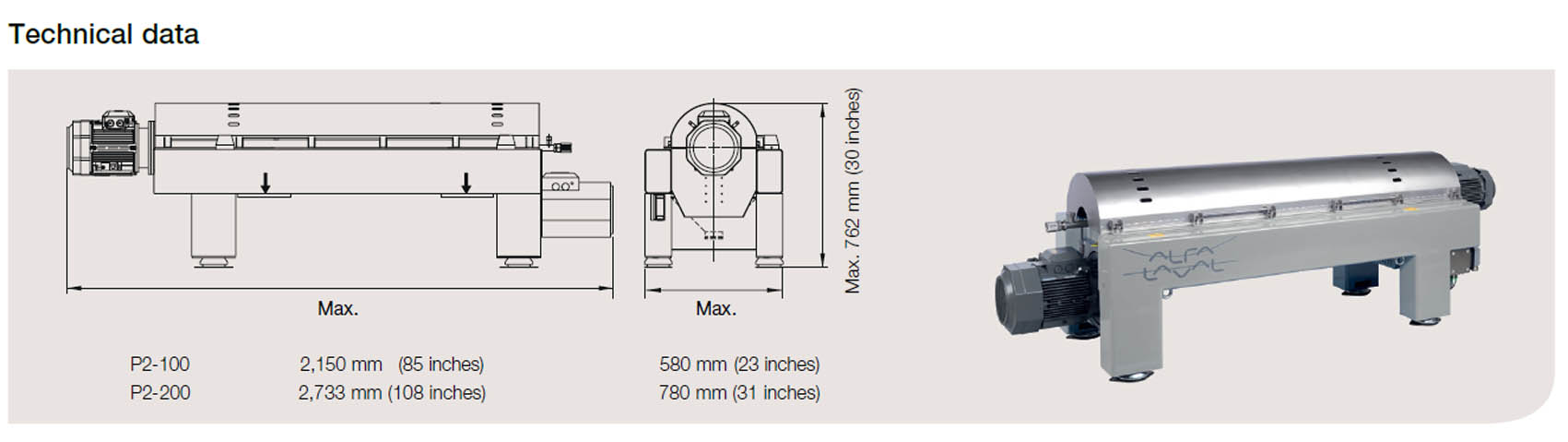
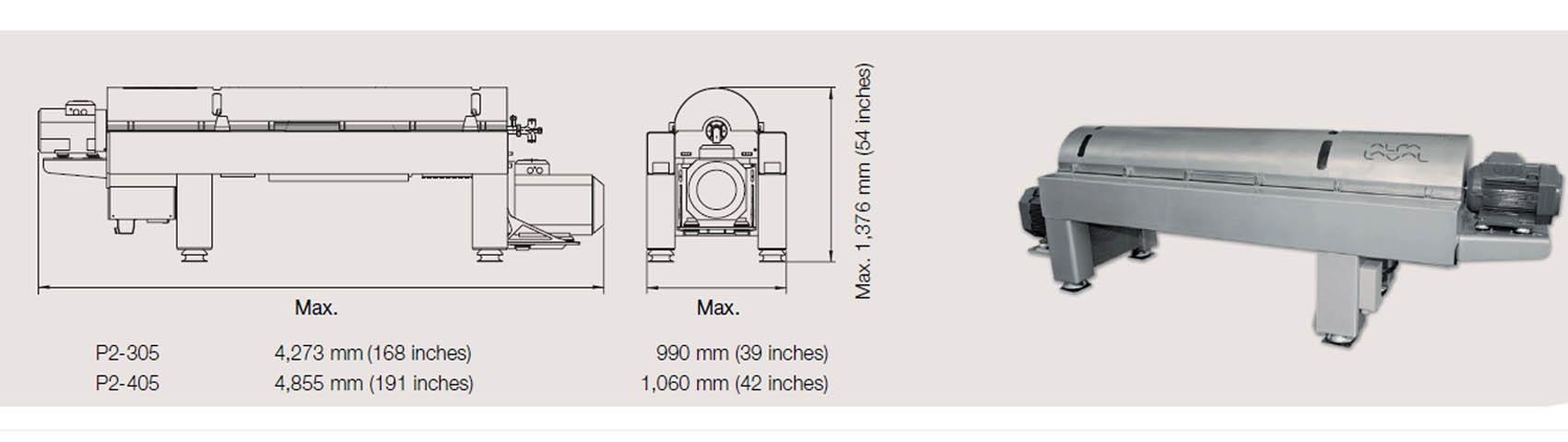
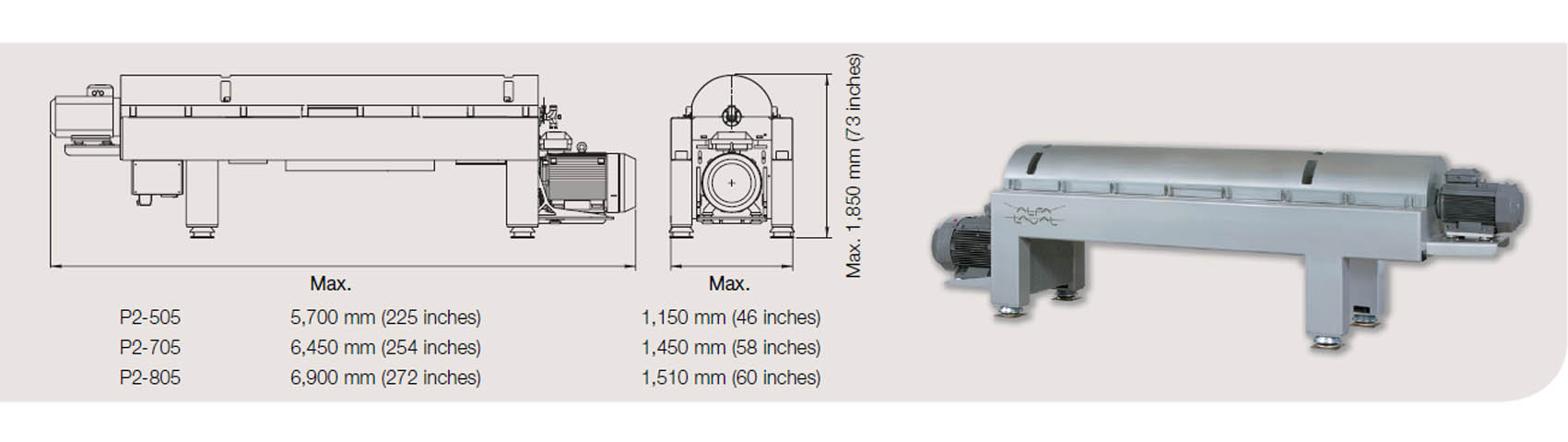
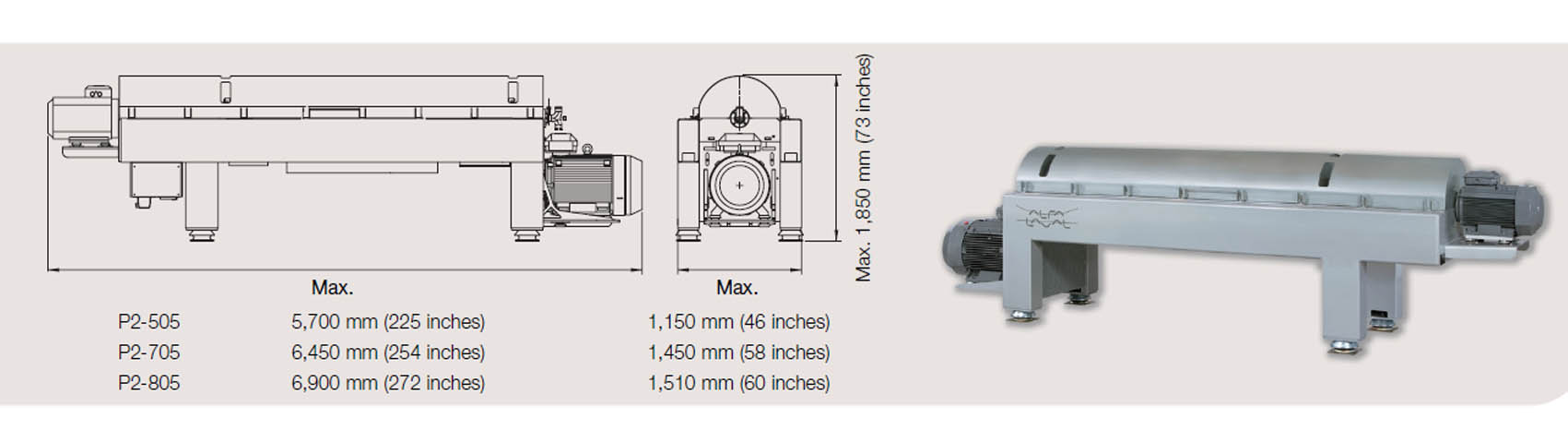